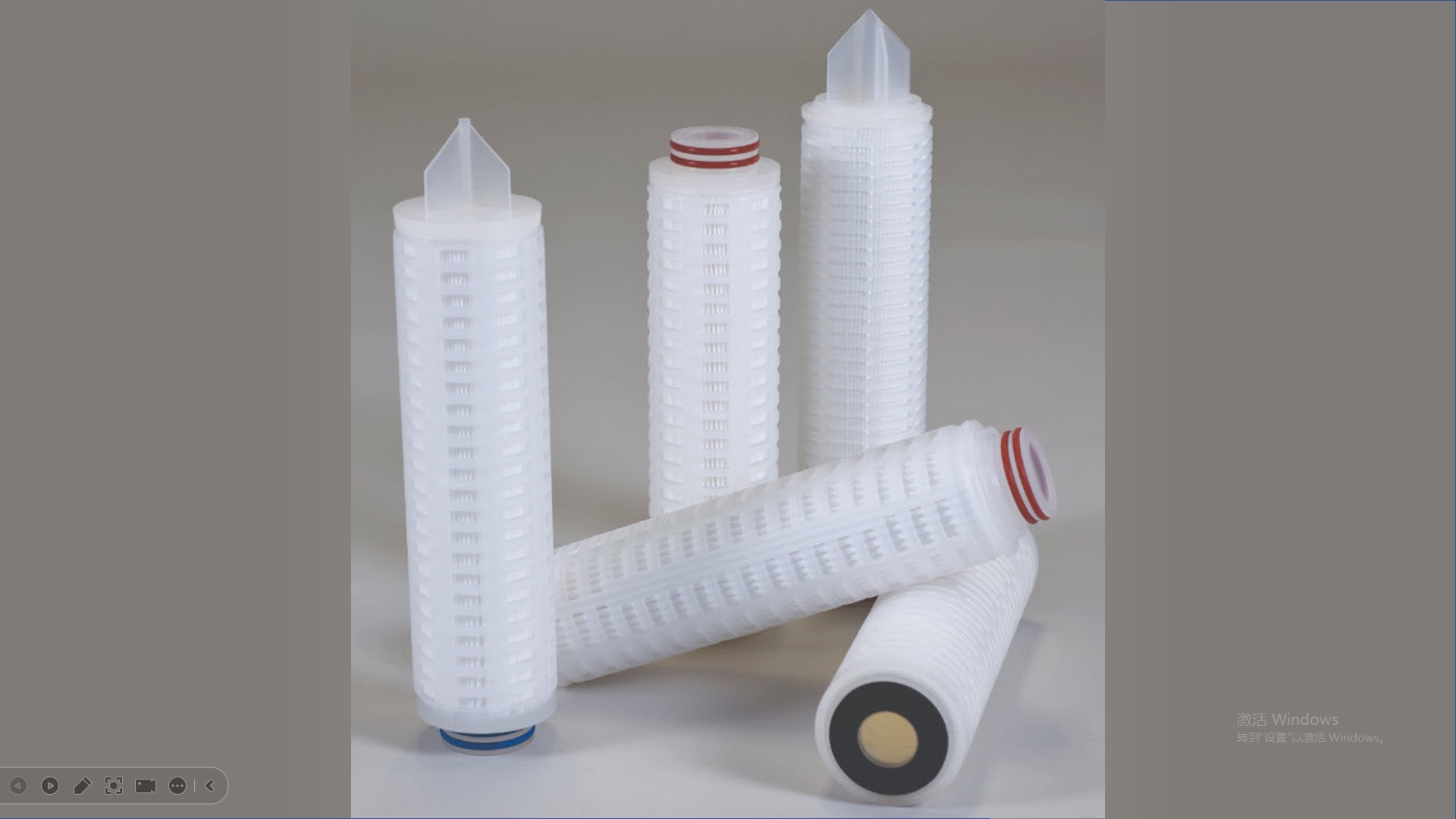
双组份热轧无纺布的行业知识及常见问答
行业知识
定义:双组份热轧是一种将两种不同材料(如不同成分的合金或金属)通过热轧工艺复合在一起的生产方法,以获得具有特定性能的复合材料。
工艺流程:包括板坯准备、加热、轧制、冷却等环节。在轧制过程中,两种材料在高温和压力作用下实现冶金结合。
材料选择:根据最终产品的性能要求,选择合适的基材和复合材料。例如,在汽车制造中,可能将高强度钢与耐腐蚀合金复合,以满足车身强度和耐蚀性的双重需求。
设备要求:需要具备精确的温度控制、强大的轧制压力以及良好的轧辊调整能力,以确保两种材料在轧制过程中能够均匀变形并紧密结合。
质量控制:通过检测复合材料的界面结合强度、尺寸精度、表面质量等指标,确保产品质量符合标准要求。
应用领域:广泛应用于汽车、航空航天、机械制造等行业,用于生产具有特殊性能要求的零部件,如汽车排气管、飞机发动机部件等。
常见问答
双组份热轧的优点是什么?
可以实现不同材料性能的优化组合,如同时具备高强度和良好的耐腐蚀性;提高材料的利用率,降低成本;通过热轧工艺使材料之间形成牢固的冶金结合,提高产品的可靠性和使用寿命。
双组份热轧过程中常见的问题有哪些?
可能出现材料界面结合不良、尺寸超差、表面缺陷等问题。这些问题可能由多种因素引起,如原材料质量问题、轧制工艺参数不合理、设备故障等。
如何解决双组份热轧中的结合不良问题?
首先要确保原材料表面清洁、无氧化皮等杂质;然后合理调整轧制温度、压力等工艺参数,使两种材料在轧制过程中能够充分变形并紧密结合;同时,加强对设备的维护和调试,保证轧辊的平行度和压力均匀性。
双组份热轧对设备有哪些特殊要求?
需要具备高精度的温度控制系统,能够准确控制加热炉和轧制过程中的温度;轧机应具有足够的轧制力和良好的轧辊调整功能,以适应不同材料的轧制需求;此外,还需要配备完善的检测设备,用于实时监测产品质量。
如何提高双组份热轧产品的表面质量?
在轧制前对原材料进行适当的表面处理,如打磨、抛光等,减少表面粗糙度;优化轧制工艺,合理控制轧制速度、压下量等参数,避免因速度过快或压下量过大导致表面缺陷;使用高质量的轧辊,并定期进行维护和更换,保证轧辊表面的光滑度。